I recently picked up a higher power charger… In my case, I chose the Revolectric FMA PL-6. This is a very highly regarded charger and I did not pick it for just the power but that was a basic requirement in the decision making process. So far, I am enjoying it and I will have another post up shortly with more info on that product. The important plot point for now is that this is a single output charger that can crank over 400W of charge power at 12V and over 800W at 24V. Compared to my previous chargers that have always (at most) been limited to 50W per output this thing is a real power house… but I was thinking I had to trade off quite a bit to get the big power. For instance…
The first big trade off when looking at these higher wattage chargers is that they typically have fewer outputs. On my old trustworthy Hitec X4 I have 4 outputs, each capable of 50W of charging power. When you start looking at chargers with 400W or so you usually get 1 output or occasionally 2 outputs with 200W of power each. By the time you get to 600W or higher you are typically going to get one output.
This was an acceptable trade off for me because my main goal in purchasing this charger was to allow me to charge my 6S 3300-4000mah LiPos in a reasonable time. A 4A charge (one hour recharge for the 4000s) at 25V (approx.) requires a 100W charger. With my 50W, charge times were in the range of 1.5-2 hours. With my new charger I can charge at 2C (8A) which at 25V is 200W and charge in 30 minutes or less. Not bad! In a pinch I can even charge faster as the batteries are rated for 5C (20A) max charge rate which would bring me to a 12 minute charge provided I have at least a 24V supply! I don’t like to push the batteries that hard normally but it’s nice to have that ability.
The problem, it would seem is that I now can only charge one battery at a time so if I charge at 2C or so I could charge another battery every 30 minutes. That’s great but it sure would be nice to be able to charge multiples… Oh well, I guess I have to give up something for progress… or do I! As it turns out there is a way to get there, and it really isn’t that difficult. Enter the parallel charging board…
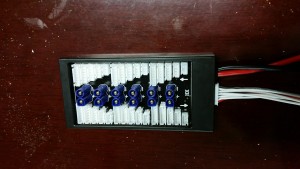
With this nifty little board plugged into the 6S balance port on the included balance board as well as the main charge ports of the PL6, I can now connect up to 6 similar batteries at a time and using the high power charging capabilities of this charger I can charge all 6 at once!! There are many versions of this board with various types of charge plugs, so be sure to get the version that is right for your batteries. It’s really fairly simple to use and quite effective. Basically as long as the batteries are all similar cell counts and are starting the charge cycle at fairly similar states of charge, you can simply plug all of them into the board (main charge lead first, then the balance plug from each battery) and you’re ready to charge.
As an example, let’s say I’ve flown 6 flights on my T28 using 3S 2200 mah LiPo batteries. Assuming I’ve run them all down near exhaustion I simply plug in the main leads and then the balance plugs to the balance board, set the charger for 2200mah charge rate as normal but specifying that I am charging 6 parallel batteries. The charger will then multiply the charge rate and start charging at 13.2A. In an hour or so, all 6 will be charged. If all the batteries can handle a 2C charge rate of 4.4A then we could charge them all in about 30 minutes as the charger would be pumping out 26.4A. 26.4A at 12V (all approximations) would require a bit over 300W which is easily attainable with even a fairly modest 12V power supply or battery.
There are a couple things to keep track of when parallel charging. You should take it seriously when I say that the batteries need to start the process at near similar charge levels. Any difference in voltage between the packs will equalize by current rushing from one pack to the other through whatever connections are available (thus the advice to connect the main load connectors first since they can handle more current). This rush of current if pretty much unrestricted and could overheat another battery or smoke the balance board if the difference is to great. Also, note that all the packs need to be of equal cell count so no mixing 3S and 6S etc…
When this really gets to be impressive is when you look at what happens if I want to charge up all six of my 6S batteries. I have 2 4000mah, 3 3300mah and 1 3700mah 6S packs for use in several of my planes. Using my old 50Wx4 charger getting all 6 packs back to charged state after a full day of flying would take at least one full charge cycle of 1.5 hours (at least) for the first four and an additional 1.5 (or more) hours for the second batch of 2. This is 3-4 hours of charging. Now, I can hook up all 6 packs in parallel and even if I pick a modest 3.3A charge rate the charger will then do the match and start charging at about 20A (assuming adequate DC power). The charge cycle will likely take only a bit over an hour and all 6 packs will be race ready again!
I’m not sure I’d want to do this with packs that were hugely different in capacity… have to think about what will happen and whether this might cause issues but I’m not concerned with this particular scenario. Of course parallel charging is possible with other chargers… this is not something only this charger can do… but to be useful the charger needs power to spare. Your average 50W charger need not apply… Here are links to both the charger and the balance board in case you are interested in purchasing one or both for yourself.